precision machining technology 3rd edition pdf
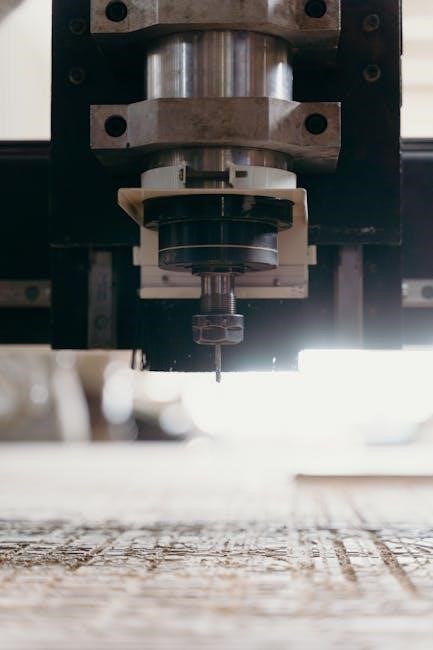
Precision machining technology involves advanced manufacturing processes to create high-precision components with minimal tolerances‚ ensuring accuracy and quality in various industries like aerospace‚ automotive‚ and healthcare.
1.1 Definition and Overview
Precision machining technology refers to the precise manufacturing processes used to create components with tight tolerances and high accuracy. It involves advanced techniques like turning‚ milling‚ drilling‚ and grinding‚ utilizing specialized machine tools and equipment. The process requires meticulous control over dimensions‚ surface finishes‚ and material properties to meet exact specifications. Precision machining is critical in industries demanding high-performance parts‚ such as aerospace‚ automotive‚ and medical devices. By combining cutting-edge tools‚ metrology‚ and quality control‚ it ensures components function reliably under extreme conditions‚ making it a cornerstone of modern manufacturing.
1.2 Importance in Modern Manufacturing
1.3 Brief History and Evolution
Precision machining traces its roots to ancient civilizations‚ where early tools were crafted for specific tasks. The Industrial Revolution marked a significant leap with mechanized lathes and milling machines. The 20th century introduced CNC machining‚ enabling precise automation. Modern advancements include multi-axis machining‚ EDM‚ and additive manufacturing‚ driven by computational power and material science. The evolution reflects humanity’s quest for accuracy‚ efficiency‚ and innovation‚ shaping industries from aerospace to healthcare. Each milestone has refined techniques‚ ensuring precision machining remains integral to manufacturing’s progress and technological advancement.
Precision machining has evolved significantly over centuries‚ transitioning from manual craftsmanship to highly automated processes. Early developments included the use of hand tools and simple machines‚ with the Middle Ages introducing mechanical clocks requiring precise components. The Industrial Revolution brought steam-powered lathes and milling machines‚ enabling mass production. The 20th century saw the rise of CNC machining‚ driven by computer-aided design (CAD) and computer-aided manufacturing (CAM). Modern advancements include multi-axis machining‚ nanotechnology‚ and additive manufacturing‚ supported by advanced materials and coatings. This evolution underscores the industry’s adaptability and innovation‚ driven by technological advancements and the demand for higher precision.
Core Concepts in Precision Machining
Precision machining involves high-accuracy processes‚ advanced tools‚ and meticulous control of materials to achieve exact dimensions and surface finishes‚ ensuring superior quality and performance in manufactured components.
2.1 Machining Processes and Techniques
Precision machining employs various advanced processes and techniques to achieve high accuracy and surface finish. Common methods include turning‚ milling‚ drilling‚ and grinding‚ each optimized for specific materials and geometries. Techniques like hard turning and micro-machining address intricate details‚ while EDM and wire EDM handle complex shapes. These processes utilize CNC machines for precision control‚ ensuring minimal material waste and adherence to tight tolerances. Proper selection of tools‚ cutting parameters‚ and coolant systems is critical for maintaining quality and efficiency in production environments.
2.2 Machine Tools and Equipment
Precision machining relies on advanced machine tools and equipment to achieve high accuracy and efficiency. Computer Numerical Control (CNC) machines‚ such as lathes‚ milling machines‚ and grinders‚ are central to modern machining. These machines utilize precision-cutting tools and are programmed to perform complex operations with minimal human intervention. Multi-axis machining centers enable the production of intricate geometries in a single setup‚ reducing production time. Additionally‚ tool holders‚ workholding devices‚ and metrology equipment like coordinate measuring machines (CMMs) ensure precise alignment and inspection of parts. Specialized equipment‚ such as EDM machines‚ is used for cutting hard or difficult-to-machine materials‚ enhancing the versatility of precision machining operations.
2.3 Metrology and Quality Control
Metrology and quality control are critical in precision machining to ensure parts meet exact specifications. Dimensional measurement tools like calipers‚ micrometers‚ and coordinate measuring machines (CMMs) verify geometric tolerances. Surface finish analysis using profilometers assesses roughness‚ while non-destructive testing (NDT) methods‚ such as ultrasonic or magnetic particle testing‚ detect internal defects without damaging components. Statistical process control (SPC) monitors production variability‚ ensuring consistency. Quality control systems‚ including ISO certifications‚ maintain standards‚ and traceability ensures each part’s history is documented. These practices guarantee precision‚ reliability‚ and compliance with industry standards‚ making metrology indispensable in achieving high-quality machining outcomes.
2.4 Material Selection and Properties
Material selection is pivotal in precision machining‚ as it directly impacts part performance and manufacturability; Properties like hardness‚ ductility‚ and thermal conductivity influence machining processes. Ferrous metals‚ such as steel‚ offer high strength but may require specialized tools. Non-ferrous metals‚ like aluminum‚ combine lightweight properties with high conductivity; Plastics and composites present unique challenges due to their heat sensitivity and anisotropic behavior. Understanding material properties ensures optimal tool selection‚ minimizes wear‚ and enhances machining accuracy. Environmental factors‚ such as corrosion resistance‚ also guide material choices. Proper material selection aligns with application requirements‚ ensuring long-term reliability and adherence to industry standards.
Advanced Topics in Precision Machining
Advanced topics explore cutting-edge technologies like multi-axis machining‚ micro/nano machining‚ and automation‚ integrating precision engineering with smart manufacturing to enhance accuracy‚ efficiency‚ and scalability in modern production.
3.1 Multi-Axis Machining and Complex Geometries
Multi-axis machining enables the production of intricate geometries by utilizing advanced CNC systems with 3 to 5 axes‚ allowing for precise cutting in multiple directions. This technology is critical for creating complex shapes in materials like aluminum‚ titanium‚ and high-performance alloys. It is widely used in aerospace‚ automotive‚ and medical industries for components requiring tight tolerances and smooth surface finishes. The integration of CAD/CAM software ensures accurate toolpath generation‚ minimizing manual intervention and reducing production time. Multi-axis machining also supports automation‚ enabling unattended operations and enhancing overall manufacturing efficiency.
3.2 Micro and Nano Machining Technologies
Micro and nano machining technologies are specialized processes for producing miniature components with sub-micron accuracy. These techniques are essential in fields like electronics‚ optics‚ and biomedical engineering. They utilize advanced tools and materials‚ such as ultra-fine grained carbides and diamond-coated tools‚ to achieve precise cuts and smooth surfaces. Applications include creating microfluidic channels‚ optical lenses‚ and medical implants. The integration of real-time monitoring systems ensures process control‚ minimizing material waste and improving yield rates. These technologies are critical for meeting the growing demand for compact‚ high-precision devices in modern industries.
3.3 Automation and CNC Machining
Automation and CNC machining are integral to precision machining‚ enhancing productivity and consistency. CNC machines use pre-programmed instructions to perform complex tasks with high accuracy. Automation integrates robots and machine learning to optimize workflows‚ reducing human intervention. These technologies improve efficiency‚ reduce errors‚ and enable 24/7 production. Advanced CNC systems incorporate real-time monitoring and adaptive control‚ adjusting parameters for optimal performance. Automation also streamlines material handling and tool changes‚ minimizing downtime. The combination of CNC machining and automation is transforming manufacturing‚ enabling the production of intricate parts with unparalleled precision. This integration is crucial for meeting the demands of modern‚ high-tech industries.
3.4 Additive Manufacturing and Hybrid Processes
Additive manufacturing (AM) revolutionizes precision machining by enabling direct production of complex geometries. AM builds parts layer-by-layer‚ reducing material waste and allowing designs impossible with traditional methods. Hybrid processes combine AM with subtractive machining‚ enhancing surface finish and accuracy. These processes integrate CNC and AM systems‚ ensuring seamless production of intricate components. They are particularly valuable in aerospace and medical fields‚ where customization and precision are critical. Hybrid manufacturing optimizes production workflows‚ reduces lead times‚ and improves part consistency‚ making it a cornerstone of modern precision machining advancements.
Applications of Precision Machining
Precision machining is crucial across industries‚ including aerospace‚ automotive‚ medical‚ and consumer electronics‚ enabling the production of high-precision‚ durable‚ and performance-critical components essential for innovation.
4.1 Aerospace and Defense Industries
Precision machining plays a pivotal role in the aerospace and defense sectors‚ where intricate components like turbine blades‚ engine parts‚ and satellite components require high accuracy. Advanced materials such as titanium and composites are machined to withstand extreme conditions‚ including high temperatures and stress. The need for zero-defect manufacturing drives the use of state-of-the-art CNC machines and metrology tools. These industries rely on precision machining to ensure reliability‚ safety‚ and performance in critical applications‚ from aircraft engines to missile guidance systems‚ making it indispensable for national security and space exploration efforts.
4.2 Automotive and High-Performance Engineering
In automotive and high-performance engineering‚ precision machining is essential for producing high-precision engine components‚ gear systems‚ and chassis parts. The automotive sector demands tight tolerances to ensure fuel efficiency‚ durability‚ and performance. Advanced machining techniques are used to craft lightweight materials like aluminum and carbon fiber‚ reducing vehicle weight while maintaining strength. High-performance racing components require customized machining solutions for optimal speed and reliability. Precision machining enables the creation of complex geometries and surface finishes‚ crucial for components subjected to intense stress‚ such as turbochargers and pistons‚ driving innovation in both mainstream and motorsport applications.
4.3 Medical and Biomedical Applications
Precision machining plays a vital role in medical and biomedical sectors‚ enabling the production of intricate‚ high-precision components for surgical instruments and implants. Machining techniques are used to create implants like hip joints‚ dental implants‚ and pacemaker components from materials such as titanium and stainless steel. Advanced methods ensure biocompatibility and durability‚ crucial for long-term patient health. Additionally‚ precision machining is used in fabricating medical devices‚ such as surgical robots and MRI components‚ requiring extreme accuracy and reliability. The ability to machine complex shapes and micro-features ensures that medical devices meet stringent safety and performance standards‚ improving patient outcomes and advancing healthcare engineering.
4.4 Consumer Electronics and Precision Instruments
Precision machining is integral to the production of consumer electronics and precision instruments‚ where miniaturization and high accuracy are critical. Techniques like micro-machining enable the creation of tiny components for devices such as smartphones‚ smartwatches‚ and optical instruments. Advanced materials and coatings are used to enhance performance and durability. Machining also plays a key role in producing high-precision optics‚ sensors‚ and semiconductor components. The ability to achieve tight tolerances ensures seamless functionality and reliability in these devices‚ driving innovation in both consumer electronics and specialized instrumentation markets‚ where precision is paramount for maintaining product quality and user satisfaction globally.
Precision Machining Techniques
Precision machining techniques involve advanced methods like turning‚ milling‚ drilling‚ and grinding to achieve high accuracy and surface finish‚ critical for producing precise components in various industries.
5.1 Turning and Milling Operations
Turning and milling are fundamental precision machining operations. Turning involves rotating a workpiece to remove material using a stationary cutting tool‚ while milling uses a rotating cutter to shape materials. Both processes require precise control over toolpaths‚ speeds‚ and feeds to ensure dimensional accuracy and surface quality. Modern CNC machines enable complex geometries and high tolerances‚ making these operations essential in producing parts for aerospace‚ automotive‚ and medical industries. Proper tool selection and machining strategies are critical for optimizing efficiency and minimizing material waste during these operations.
5.2 Drilling and Boring Processes
Drilling and boring are precision machining processes used to create or enlarge holes in workpieces. Drilling involves using a rotating drill bit to generate holes‚ while boring employs a single-point cutting tool to enlarge existing holes for high accuracy. These processes are critical for achieving precise diameters‚ straightness‚ and surface finishes. Advanced techniques‚ such as pilot drilling and internal boring‚ ensure minimal material waste and optimal results. Both processes are widely applied in manufacturing to produce components for industries like aerospace‚ automotive‚ and medical devices‚ where tight tolerances and precision are essential.
5.3 Grinding and Polishing Techniques
Grinding and polishing are precision machining processes used to achieve high surface finish and dimensional accuracy. Grinding involves using abrasive wheels to remove material‚ while polishing uses finer abrasives or chemical methods to create smooth surfaces. These techniques are essential for removing micro-scratches‚ enhancing surface quality‚ and preparing parts for final assembly. Advanced grinding methods‚ such as creep-feed grinding‚ optimize material removal rates. Polishing often follows grinding to attain mirror-like finishes‚ reducing friction and preventing corrosion. Both processes are critical in manufacturing components for aerospace‚ automotive‚ and medical industries‚ where surface integrity and precision are paramount.
5.4 Electrical Discharge Machining (EDM)
Electrical Discharge Machining (EDM) is a non-traditional machining process that removes material using electrical discharges (sparks) between a tool and a workpiece. It is ideal for machining hard‚ brittle‚ or difficult-to-cut materials like carbide and hardened steel. EDM does not require physical contact‚ eliminating mechanical stress and deflection. Key applications include creating complex cavities‚ dies‚ and molds. There are two main types: sinker EDM (ram EDM) for shaping cavities and wire EDM for cutting thin sections. EDM is widely used in aerospace‚ automotive‚ and mold-making industries due to its ability to achieve intricate geometries with high precision and surface finish.
Tools and Tooling in Precision Machining
Precision machining relies on specialized tools and tooling‚ ensuring high precision and efficiency. Cutting tools‚ like carbide inserts‚ are vital for tight tolerances and superior finishes.
6.1 Cutting Tools and Coatings
In precision machining‚ cutting tools are designed for high accuracy and durability. Tungsten carbide and cubic boron nitride are common materials due to their hardness. Coatings like TiAlN enhance tool life by reducing wear and friction‚ improving thermal resistance. Advanced coatings minimize tool degradation‚ ensuring consistent performance. Proper tool selection and coating application are critical for optimizing machining processes‚ reducing downtime‚ and achieving desired surface finishes. These tools are essential for meeting precise specifications in various industries‚ ensuring efficiency and quality in production.
6.2 Tool Holders and Workholding Devices
Tool holders and workholding devices are critical for maintaining precision and stability in machining operations. These devices securely hold cutting tools and workpieces‚ ensuring accurate alignment and minimizing vibration. Precision-engineered tool holders‚ such as collet chucks and hydraulic clamps‚ provide rigid clamping forces‚ preventing tool slippage. Workholding devices like vises‚ fixtures‚ and vacuum clamps are tailored to specific workpiece geometries‚ enabling precise control. Advanced materials and designs enhance durability and versatility‚ while modular systems allow quick tool changes‚ improving efficiency. Proper selection and maintenance of these devices are essential for achieving high-quality surface finishes and dimensional accuracy in precision machining applications.
6.3 Custom Tooling Solutions
Custom tooling solutions are tailored to meet specific machining requirements‚ offering enhanced performance and efficiency for unique part geometries. These specialized tools address challenges not met by standard tools‚ reducing production time and improving part quality. Collaborative efforts between manufacturers and machinists ensure tools are designed for precise fit and function. Advanced materials and coatings extend tool life‚ while modular designs allow adaptability. Custom solutions often integrate automation features‚ streamlining workflows. Their application is critical in high-precision industries like aerospace and medical‚ where specialized components require exacting tolerances. Investing in custom tooling can significantly optimize manufacturing processes and yield superior results. Precision machining relies heavily on such innovations.
6.4 Tool Maintenance and Optimization
Tool maintenance and optimization are critical for extending tool life and ensuring consistent machining performance. Regular inspection identifies wear and tear‚ preventing tool failure mid-operation. Coatings and surface treatments enhance durability‚ while proper storage minimizes damage. Optimizing tool geometry and cutting parameters reduces wear and improves efficiency. Automation tools help monitor and predict tool life‚ enabling proactive replacements. Maintenance programs include cleaning‚ sharpening‚ and recalibration‚ ensuring tools remain within precise specifications. Effective optimization reduces downtime‚ lowers costs‚ and improves product quality. Continuous improvement strategies refine these practices‚ driving operational excellence in precision machining environments. Regular audits ensure adherence to maintenance schedules‚ safeguarding production consistency and accuracy. Proper tool care is essential for sustainable manufacturing.
Metrology and Inspection in Precision Machining
Metrology and inspection ensure precision machining meets strict tolerances and quality standards‚ utilizing advanced measurement tools and techniques to verify dimensional accuracy and surface finish integrity.
7.1 Dimensional Measurement Techniques
Dimensional measurement techniques in precision machining involve precise tools like calipers‚ micrometers‚ and coordinate measuring machines (CMMs) to ensure components meet exact specifications. These tools measure linear dimensions‚ such as length‚ width‚ and height‚ with high accuracy. Optical measurement systems‚ including vision systems and laser scanners‚ are also used for intricate geometries. Proper calibration and operator expertise are crucial to maintain measurement reliability. Such techniques are essential in industries requiring tight tolerances‚ ensuring final products function as designed and meet quality standards. Regular verification of measurements prevents defects and enhances overall manufacturing efficiency. Accurate dimensional control is vital for product performance and durability.
7.2 Surface Finish and Roughness Measurement
Surface finish and roughness measurement are critical in precision machining to ensure components meet quality and performance standards. Techniques like profilometry and surface roughness testers measure parameters such as Ra (arithmetic mean roughness) and Rz (mean roughness depth). Proper surface finish reduces friction‚ wear‚ and corrosion‚ enhancing component functionality. Advanced tools provide detailed profiles‚ identifying imperfections and ensuring compliance with specifications. Accurate measurement is essential for maintaining product quality‚ reliability‚ and longevity. Surface finish assessment is a key step in quality control‚ directly impacting the final product’s performance and durability in various industrial applications.
7.3 Geometric Tolerancing and Standards
Geometric tolerancing defines allowable variations in the shape‚ size‚ and position of features on a part. It ensures interchangeability and functionality by specifying limits for features like angles‚ diameters‚ and surface orientations. Standards such as ISO 1101 and ASME Y14.5 provide frameworks for applying these tolerances. Proper tolerancing prevents assembly issues and ensures precision in manufacturing. By adhering to these standards‚ manufacturers maintain consistency and quality‚ reducing errors and improving product reliability. Geometric tolerancing is a cornerstone of precision machining‚ enabling the creation of parts that meet exacting specifications and perform optimally in their intended applications.
7.4 Non-Destructive Testing (NDT) Methods
Non-destructive testing (NDT) methods are essential in precision machining to evaluate components without causing damage. Techniques like ultrasonic testing‚ magnetic particle testing‚ and liquid penetrant testing detect surface and internal defects. Radiography uses X-rays or gamma rays to inspect internal structures‚ while thermal imaging identifies temperature variations. Acoustic emission testing monitors high-frequency sounds from material stress. These methods ensure compliance with quality standards‚ prevent defects‚ and maintain part integrity. NDT is critical for high-performance industries like aerospace and healthcare‚ where component failure can have severe consequences; By integrating NDT‚ manufacturers ensure reliability‚ safety‚ and optimal performance of precision-machined parts.
Materials and Their Machinability
Understanding material properties is crucial for effective machining. Ferrous and non-ferrous metals‚ plastics‚ and composites each have unique machinability characteristics. Factors like hardness‚ thermal conductivity‚ and tool wear influence machining efficiency and accuracy.
8.1 Ferrous and Non-Ferrous Metals
Ferrous metals‚ such as steel and cast iron‚ contain iron and are widely used due to their strength and durability. Non-ferrous metals‚ including aluminum‚ copper‚ and titanium‚ are valued for their corrosion resistance and conductivity. Machining these metals requires specific tools and techniques. Ferrous metals often require harder cutting tools due to their high strength‚ while non-ferrous metals may demand specialized coatings to prevent tool wear. Understanding the properties of each metal type is essential for achieving precise cuts and maintaining tool longevity in precision machining applications.
8.2 Plastics and Polymer Materials
Plastics and polymer materials are increasingly used in precision machining for their versatility and cost-effectiveness. These materials can be easily shaped into complex forms‚ making them ideal for applications in consumer electronics‚ medical devices‚ and automotive components. Unlike metals‚ plastics are less abrasive‚ reducing tool wear‚ but they can deform under heat or stress. Machining techniques such as milling and turning must be carefully optimized to maintain dimensional accuracy and surface finish. Additionally‚ the use of appropriate cutting tools and coolants is essential to prevent melting or dimensional instability during the machining process.
8.3 Composites and Advanced Materials
Composites and advanced materials‚ such as carbon fiber reinforced polymers (CFRP) and glass fiber composites‚ are widely used in precision machining for their high strength-to-weight ratios and resistance to corrosion. These materials are particularly favored in aerospace and automotive industries where lightweight and durability are critical. However‚ machining composites poses challenges due to their heterogeneous structure‚ which can lead to delamination and fiber pullout. Specialized cutting tools‚ such as diamond-coated tools‚ and precise control of machining parameters are essential to achieve desired surface finishes and maintain material integrity. Proper techniques ensure optimal performance and longevity of the final product.
8.4 Exotic and High-Temperature Alloys
Exotic and high-temperature alloys‚ such as Inconel‚ Waspaloy‚ and Rene 41‚ are engineered for extreme environments‚ offering exceptional resistance to heat‚ corrosion‚ and wear. These alloys are critical in aerospace‚ power generation‚ and industrial applications where high thermal stability is essential. Machining these materials requires specialized tools‚ such as carbide or ceramic inserts‚ due to their hardness and ability to maintain strength at elevated temperatures. Coolant strategies and optimized machining parameters are crucial to prevent thermal damage and ensure dimensional accuracy. Their unique properties make them indispensable in high-performance systems‚ despite the challenges they present during manufacturing processes.
Precision Machining in Modern Industry
Precision machining drives modern industry through advanced technologies‚ enabling high-efficiency production of complex components. Automation‚ CNC systems‚ and sustainable practices are key to meeting global demand for precision products.
9.1 Industry 4.0 and Smart Manufacturing
Industry 4.0 integrates advanced technologies like IoT‚ AI‚ and big data analytics into manufacturing‚ enhancing precision machining through smart factories. Real-time monitoring and predictive maintenance optimize production efficiency‚ reducing downtime. CNC machines communicate seamlessly‚ enabling adaptive production systems. Smart manufacturing fosters data-driven decision-making‚ improving product quality and traceability. This digital transformation supports personalized products and faster time-to-market‚ aligning with global trends in automation and sustainability. Precision machining embraces these innovations‚ ensuring high-performance components for modern applications. Industry 4.0 revolutionizes manufacturing processes‚ driving growth and competitiveness in the global market.
9.2 Digital Twin Technology in Machining
Digital twin technology replicates physical machining processes in a virtual environment‚ enabling real-time monitoring and simulation. This technology enhances precision by optimizing tool paths‚ reducing errors‚ and predicting wear. By integrating IoT and AI‚ digital twins improve process efficiency and product quality. They allow operators to test scenarios virtually‚ minimizing downtime and material waste. Predictive maintenance is another key benefit‚ as digital twins analyze equipment performance to prevent failures. This technology aligns with Industry 4.0 goals‚ fostering smarter‚ data-driven machining practices. As a result‚ digital twins are revolutionizing precision machining‚ ensuring higher accuracy and sustainability in modern manufacturing environments.
9.3 Sustainability and Green Machining Practices
Sustainability in precision machining focuses on reducing environmental impact through eco-friendly practices. Green machining involves using minimal coolant‚ recycling materials‚ and optimizing energy consumption. Modern techniques like dry machining and minimum quantity lubrication reduce waste. Renewable energy sources and energy-efficient machinery further lower carbon footprints. Recycling of metal scraps and responsible disposal of chemicals ensure environmental compliance. These practices not only minimize ecological damage but also enhance cost-efficiency for manufacturers. By adopting green machining‚ industries contribute to global sustainability goals while maintaining high production standards and meeting regulatory requirements. This approach is critical for a sustainable future in manufacturing.
9.4 Economic Impact and Global Trends
Precision machining significantly influences the global economy by driving innovation and enabling high-tech industries. Its applications in aerospace‚ automotive‚ and healthcare foster technological advancements. Emerging markets and advancements in automation are reshaping the industry. The rise of Industry 4.0 and smart manufacturing boosts efficiency and productivity. Economic trends show increased demand for high-precision components‚ fueling market growth. Trade dynamics and supply chain optimizations further impact the sector. As global competition intensifies‚ precision machining remains a cornerstone of modern manufacturing‚ supporting economic development and industrial progress worldwide. This sector’s evolution will continue to shape global economic landscapes and technological innovation.